A collective change
Exploring the far-reaching potential of new, green fuels is a hugely important part of the decarbonisation work that is happening at DFDS. However, switching to alternative energy sources is just the transition part of our planet’s journey to net-zero. Looking at the global picture, at least a quarter of the emissions human beings need to save in order to reach that destination must come from using less energy; and actually, in the West, it’s more like 50%.
So what is DFDS doing, across its operations, to manage its own energy use more efficiently? The answer is: whatever it can. In every part of the business, a decarbonisation narrative is being written, and every member of the organisation is actively encouraged to contribute. From small shifts in behaviour to large-scale technological solutions, change is happening…
Case study 1: Tyre technology
Tyre pressure makes a significant difference to the energy efficiency of a truck and trailer combination. When the pressure is optimal, not only is rolling resistance - and thus, fuel consumption - reduced, but it also means that tyres will be correctly positioned on surfaces, so there is less wear and increased tyre life.
This much we know; the challenge comes in identifying exactly when tyre pressure becomes less than optimal. Working with partners Continental and Volvo, DFDS has been developing a system that ensures constant monitoring of tyres, with the goal of maintaining the right pressure at all times. “We’re still in the pilot phase,” observes Carl-Johan Ejserholm, Fleet Manager for DFDS Logistics Services in Gothenburg. “However, we are seeing very pleasing levels of energy consumption reduction, which is what we expected. The more data we have about our vehicles in operation, the better able we are to make decisions that will maximise efficiency.”
Case study 2: Trailer technology
With a modern, flexible fleet of over 800 refrigerated trailers, DFDS is rightly proud of the flexible, safe and efficient refrigerated transport solutions it can offer to customers. However, it’s a fuel-hungry business: a diesel-engined reefer trailer uses approx 1.4 litres per hour when the fridge is in use and cooling the trailer to -22°C. This equates to 3.68 kg per hour of CO2e. At 2200 hours per year of diesel engine fridge running time, this means emissions at the rate of 8.1 tonnes of CO2e per year, per trailer - a footprint DFDS is determined to reduce.
“Since September 2024, we’ve been testing a Thermoking/BPW regenerative axle and electric fridge unit, which has been fitted to a reefer trailer,” explains UK-based Engineering Manager Michael Robinson. “It has no diesel engine and relies on battery power to power the fridge when on the road. We’ve also purchased ten electric fridge units for trailers from Sunswap. These trailers have batteries to power the fridge, as well as solar panels on the roof to assist in battery charging; we are very excited to track the CO2e savings we’ll be making.” Read more about this solution here.
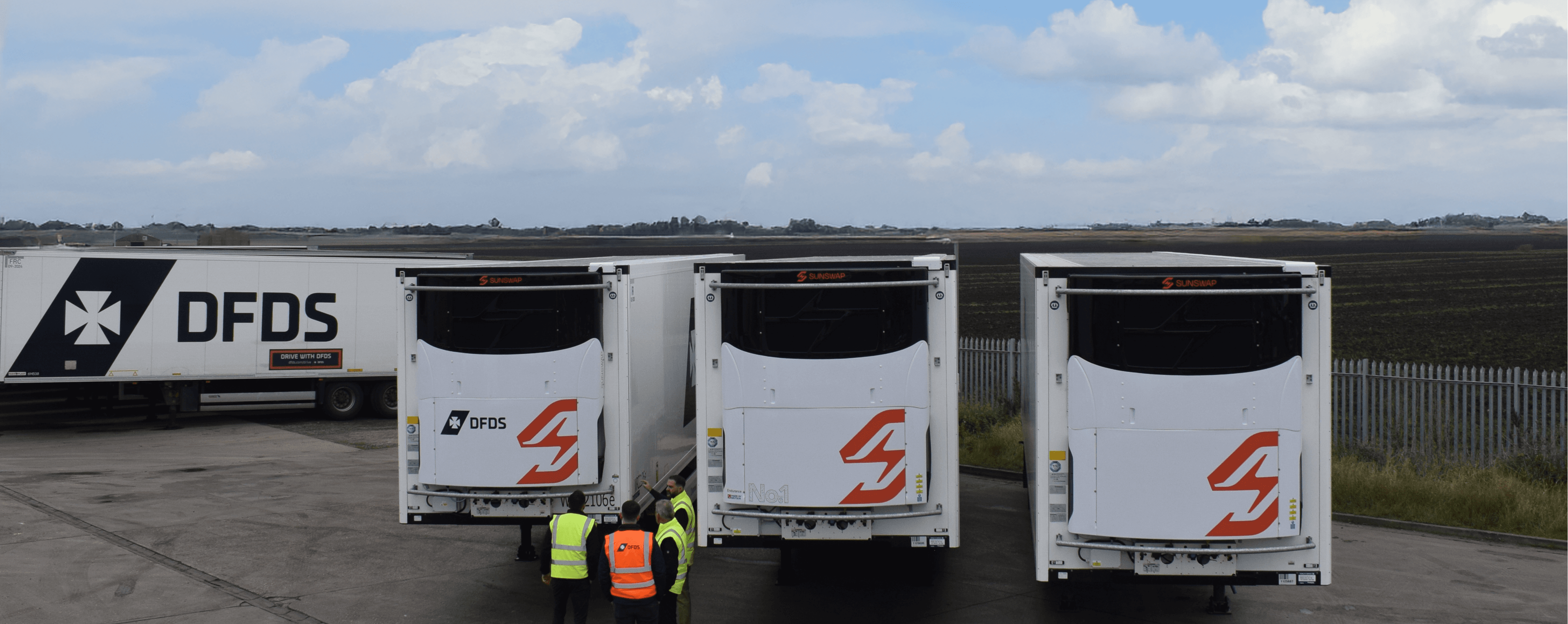
Case study 3: Ballast optimisation
To ensure stability while in operation, ships need to carry ballast water onboard. Naturally, the quantity and distribution of ballast water will vary, depending on what the ship is carrying, and how the weight of the cargo can be distributed (for maximum stability, the heaviest cargo should ideally be placed on lower decks along the centreline of the vessel).
However, to maintain speed of operation and respect designated zones for cargo types, and due to limited data-availability, cargo positioning onboard is a manual process, which means that ships must carry excess ballast water to have a stability buffer. Excess ballast water increases the draft of the vessel, creating more drag, thus consuming more fuel at sea and increasing harmful emissions.
Matthew Penistone, Senior Product Owner at HQ in Copenhagen, and his DFDS team are working on a data-driven approach to create an automated loading planner, which will help to optimise the cargo distribution onboard the vessels, reducing the need to carry excess ballast water, leading to less fuel consumption and ultimately, fewer emissions at sea.
“There’ll be additional benefits, too,” points out Penistone. “For example, we’ll have better visibility of exact cargo location and weights onboard, helping speed up the loading/unloading process and giving ship crew better visibility on cargo carried. What’s more, less ballast water being discharged will reduce the harmful impact on biodiversity of the discharge process.”
Case study 4: Microgrids
A microgrid is a small, self-contained energy system that can generate, store, and distribute electricity to meet the needs of a specific area or group of users. They can operate in ‘island mode’ or be connected to the main grid - the advantage of the latter option is that it enables buying and selling of energy, and selling of load balancing and other services to the grid, timed to get the optimum price; making microgrids an extremely attractive option commercially. “At our Vlaardingen terminal and our logistics site in Karlshamn, we’re in the process of scoping two microgrid projects,” explains Vice President and Head of Decarbonisation Sophie-Kim Chapman. “These combine a focus on producing a large percentage of our own electricity from renewables, with battery storage and a connection to the utility grid. At both sites, we anticipate increased electricity consumption – in Vlaardingen, due to the introduction of shorepower and electrified terminal equipment, and in Karlshamn, through charging for electric trucks. These projects aim to support our electrification journey, radically reduce emissions and – for our neighbours – improve air quality and mitigate grid congestion.”
Case study 5: Every Minute Counts
"Every Minute Counts" is an ambitious schedule optimisation initiative underway right across DFDS's fleet, aimed at enhancing operational efficiency while advancing the organisation’s sustainability goals. The primary objective is to reduce fuel consumption intensity by lowering the fuel oil consumed per nautical mile (kg/NM) during voyages.
This is achieved by optimising sailing speeds and operational schedules to extend time at sea, while reducing port turnaround time. “By refining our schedules, we not only improve fuel efficiency, but also significantly cut greenhouse gas emissions per voyage,” explains Cpt. Hasan Göler, Senior Vessel Performance Manager at DFDS HQ. It’s an initiative that aligns closely with the International Maritime Organisation's (IMO) strategy to decarbonise shipping.
To drive this transformation, route schedules are being carefully reevaluated and fine-tuned to achieve the optimal balance between fuel efficiency and operational requirements. Weekly reports track year-to-date progress against previous benchmarks, ensuring transparency and fostering a clear understanding of the improvements achieved.
“I believe "Every Minute Counts" highlights the critical role of data-driven decision-making, operational transparency, and a commitment to rethinking optimisation strategies for our routes,” observes Hasan. “This initiative not only demonstrates our commitment to operational excellence, but also underscores our contribution to a more sustainable future for maritime transport.”
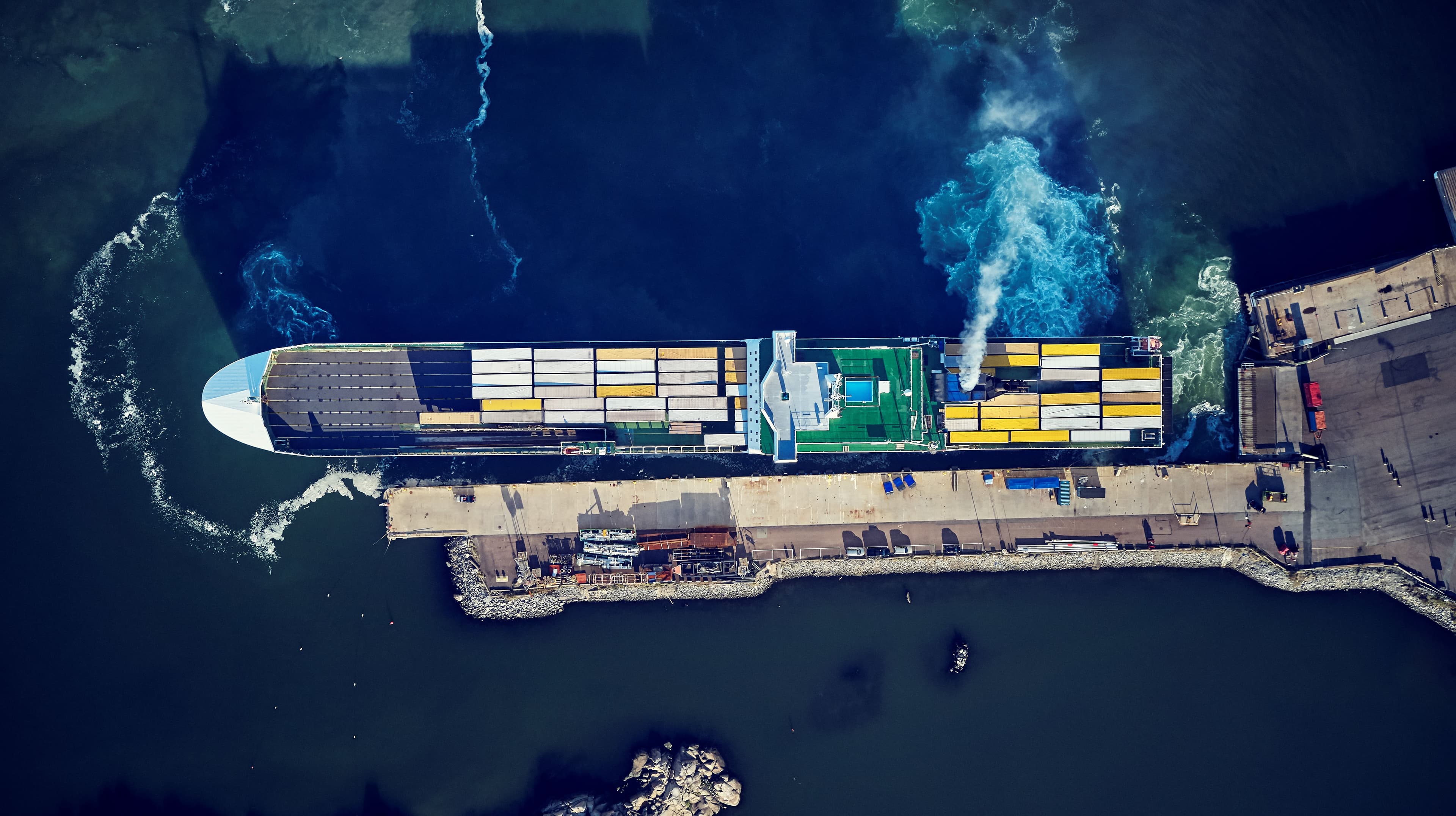
Case study 6: Cold storage energy optimisation
For obvious reasons, cold storage locations come with high energy consumption requirements; but that doesn’t mean savings can’t be made. “It’s a question of monitoring,” says Projects and Continuous Improvement Coordinator Esther Kabiito from Liverpool. “At the moment, the process is largely manual, and so we aren’t always aware of the drivers behind high consumption. To tackle this, we’re investigating a range of digital solutions, supported by AI, that can help us monitor our consumption remotely, and understand where action is needed, as well as measure the impact of any changes that we make.”
These adjustments might be ‘quick wins’ - relatively small behaviour changes on site, such as ensuring closed doors at all times, that will reduce energy consumption; or larger projects, like changing the refrigeration plant. For example, in Liverpool, an old ammonia plant has been replaced by a new, more efficient model, resulting in an energy consumption reduction of around 19% during 2023-2024.
Case study 7: Zoning of Riverside Terminal, Immingham
Improving energy efficiency isn’t always about introducing new and/or better technology. Sometimes, it’s a case of looking carefully at what is happening already, then taking a step back and seeing the possibility for something different. Take DFDS’s Riverside Terminal at Immingham, England, for example. Currently, it operates in a non-zonal manner, with cargo to and from each destination all mixed up together. “This leads to an increase in cycle time, and not enough dual cycling of units,” points out Immingham’s Director of Operations Jonathan Lowden.
To address this situation, the terminal’s layout is being given a redesign, organising it into three distinct zones: Rotterdam, Gothenburg and Esbjerg. This simple but fundamental change will ensure that cargo for each destination - both import and export - is handled much more efficiently. “We expect there to be a reduction in cycle time of around 25%, as well as a 25% increase in dual cycling,” says Lowden. This would be the equivalent of saving ~38,000 litres of fuel, or reducing ~100 tonnes of CO2e per annum.”
Case study 8: Tug masters’ speed reduction and idle times
Also at Immingham, Terberg telematics units onboard ten of DFDS’s tugs have enabled the team to carry out advanced analyses with the aim of identifying opportunities to improve energy management.
“The telematics system has helped us pick up two areas where we think efficiencies could be made,” explains Business Performance Manager George Tandiko. “By optimising the driving speed of our tugs, and minimising their engine idling time, we should be able to make considerable fuel savings.” According to pilot tests, bringing the maximum speed down from 18mph to 15mph for all tugs could reduce overall fuel consumption by 163,000 litres per annum - a CO2e saving of 438 tonnes; whilst cutting the idle time by 12% is expected to generate an annual fuel savings of 24,405 litres of fuel across the tug fleet, leading to an annual CO2e reduction of 78.5 tonnes.